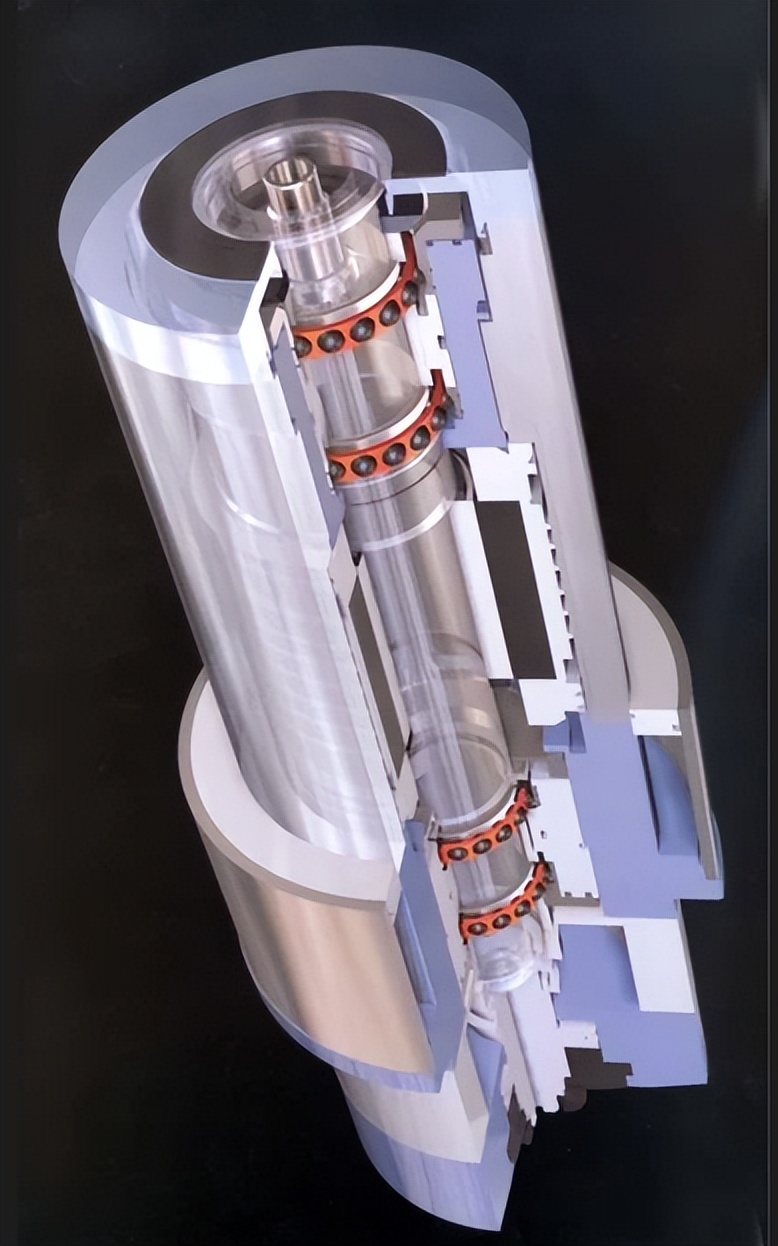
主轴轴承作为现代高精密机床的核心功能部件,其性能直接决定了加工系统的精度极限、动态响应能力以及工艺可靠性。在高端制造领域,主轴轴承已从单纯的支撑元件演变为集机械动力学、材料科学和热管理技术于一体的复杂系统。本文将深入剖析主轴轴承的技术内涵及其在先进制造中的应用逻辑。
一、主轴轴承的工程学本质
主轴轴承本质上是一个精密力流管理系统,其核心功能体现在三个维度:
- 运动引导:通过多体接触动力学模型,将主轴的非线性运动转化为受控的刚体运动
- 载荷传递:构建稳定的力流通道,将切削力、惯性力等复合载荷传导至机床基础结构
- 动态稳定:抑制高速旋转时产生的振动模态,维持工艺系统的动态刚度
这种功能实现依赖于其特殊的拓扑结构:由内外圈构成的约束边界、精密排列的滚动体构成的力传递网络、以及保持架形成的运动协调机构,共同构成了一个封闭的力学系统。
二、关键技术参数体系
- 接触角动力学
- 15°标准角设计实现了径向/轴向刚度比的最优解
- 大接触角(25°以上)方案通过增加赫兹接触面积提升轴向承载力
- 双列角接触轴承的相位匹配技术可消除力矩耦合效应
- 预紧力工程
- 恒压预紧:通过弹性元件维持稳定的接触应力
- 定位预紧:精密尺寸链构建的刚性预载荷
- 预紧力的热补偿算法:抵消高速运转时的热膨胀效应
- 系统刚度合成
- 轴承本体刚度:取决于材料弹性模量和接触几何
- 界面刚度:包含配合公差、连接件刚度等影响因素
- 动态刚度:与转速相关的阻抗特性
三、先进轴承技术演进
- 混合陶瓷轴承:
- 氮化硅(Si3N4)球体使DN值突破3.0×10^6 mm·r/min
- 热膨胀系数差实现温度自补偿效应
- 绝缘特性避免电腐蚀问题
- 磁悬浮辅助技术:
- 主动电磁轴承与机械轴承的混合支撑架构
- 振动主动抑制带宽提升至2000Hz以上
- 实现亚微米级的运动精度控制
- 智能轴承系统:
- 嵌入式传感器网络实时监测接触应力状态
- 基于应变片阵列的载荷分布重构技术
- 数字孪生驱动的剩余寿命预测模型
四、应用挑战与解决方案
- 热-力耦合难题:
- 采用梯度材料设计:外圈高导热合金+内圈低膨胀合金
- 开发新型热障润滑脂(如聚醚醚酮基润滑体系)
- 计算流体动力学优化的喷射冷却通道
- 极端工况适应:
- 五轴加工中心的摆头轴承需承受复合弯矩载荷
- 解决方案:三维曲面滚道设计+自适应预紧机构
- 重载切削场合应用串联轴承组配技术
- 精度寿命平衡:
- 表面织构技术降低摩擦系数(激光微凹坑加工)
- 开发自修复涂层(含纳米WS2的DLC涂层)
- 基于粒子滤波算法的精度衰退预测
五、维护技术前沿
- 状态监测体系:
- 多物理量融合监测(振动+声发射+温度+电流)
- 边缘计算驱动的实时故障诊断
- 基于深度学习的异常模式识别
- 再制造技术:
- 等离子喷涂修复滚道微观损伤
- 选择性激光熔覆恢复尺寸精度
- 分子级表面活化处理技术
- 润滑革命:
- 固态润滑技术(二硫化钼纳米线植入)
- 微量润滑系统(MQL)与轴承密封的协同设计
- 智能润滑剂(粘度随温度/剪切率自适应变化)
结语
主轴轴承技术正在经历从机械元件向智能功能系统的转型。未来发展趋势将呈现多维融合特征:材料基因组工程加速新型轴承钢开发、数字孪生技术实现全生命周期管理、量子传感技术突破精度测量极限。在工业母机走向纳米级精度的进程中,主轴轴承将继续扮演关键使能技术的角色,其技术进步将重新定义精密制造的边界。